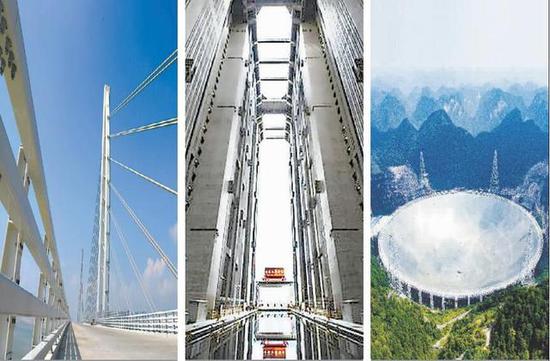
9月18日,世界上技術難度最高、規(guī)模最大的升船機——三峽升船機正式進入試通航階段。這也是世界最大水利樞紐三峽工程的最后一個建設項目。9月25日,歷時22年設計和建造,有“天眼”之稱的500米口徑球面射電望遠鏡(FAST)在中國貴州正式啟用。9月27日,全球最長跨海大橋——港珠澳大橋主體橋梁正式貫通。
半個月內,中國的超級工程不斷刷新世界之最。令人振奮的是,武漢企業(yè)參與了上述三項超級工程設計和建設,為中國建設貢獻了武漢力量。
武船為中國“天眼”做出突出貢獻
精準吊裝4450塊反射面板
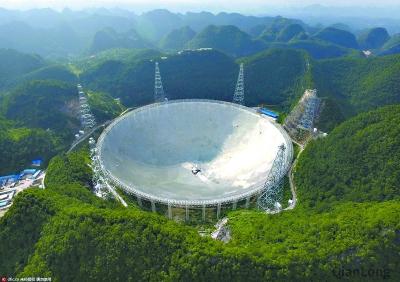
9月25日,世界最大的500米口徑球面射電望遠鏡(FAST)落成啟用儀式在貴州平塘隆重舉行,這個全球矚目的“天眼”終于睜開了眼睛。它眼望無數(shù)星辰,將人類探知宇宙奧秘的視野擴大至宇宙邊緣,同時將在未來20-30年保持國際領先水平。
FAST背后凝聚了無數(shù)科學家和建設者的智慧和汗水,同樣也離不開武船人孜孜不倦的追求、堅持不懈的努力。
武船承擔的反射面單元安裝工程即被公認為是其建造過程中的三大難題之一。FAST工程4450塊反射面單元的安裝位置分布在口徑500米的球面索網(wǎng)、離地面高度4.3米-50米不等的空間節(jié)點盤上,吊裝空間跨度、幅度之大前所未有;反射面單元為鋁合金管件桁架結構,共計216種類型,分三角形和異形四邊形兩種形狀,在空中安裝過程中需嚴格控制反射面單元的變形和精度;反射面安裝過程中還與其他工程子系統(tǒng)存在干涉和成品保護問題等,這都需拿出一攬子解決辦法和措施。
今年7月3日上午11時45分,F(xiàn)AST最后一塊反射面單元成功吊裝,F(xiàn)AST主體工程順利完工。最后的吊裝技術十分尖端,與其他各塊間距為56毫米,每一個螺栓間距1毫米。長江日報記者曾見證了最后一塊反射面單元成功吊裝的全過程。反射面單元安裝提前工期一個月完工,且在歷時311天的施工中未發(fā)生一起安全事故,武船的質量和信譽得到了業(yè)主和現(xiàn)場各方的高度評價。
8月底,F(xiàn)AST安裝工程如期進行了竣工驗收,并得到驗收組的肯定和好評。
通過FAST安裝工程,全面提升了武船特種設備的安裝能力,目前已授權專利4項,受理專利2項,申報技術創(chuàng)新課題成果1項。
武船也因此獲得了中科院國家天文臺頒發(fā)的優(yōu)秀項目部、突出貢獻單位榮譽稱號。
武船承制世界最大“船舶電梯”
40分鐘可送船通過三峽大壩
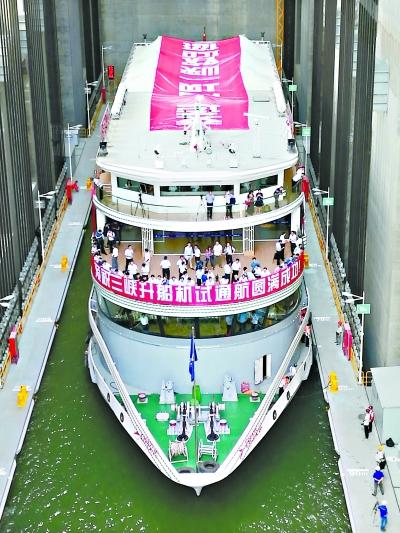
今年9月18日15時20分,隨著“船只可以進船廂”廣播的響起,長江三峽9號船緩緩駛入三峽升船機承船廂,從大壩上游到達下游,標志著三峽工程“收官之作”、武船集團參與建造的世界最大升船機——三峽升船機正式進入試通航階段。
本次試通航為期半年,為三峽升船機正式通航的前期階段,在試通航過程中將逐步提高三峽升船機運行的穩(wěn)定性和可靠性。
船舶“坐電梯”40分鐘過三峽大壩
三峽升船機過船規(guī)模3000噸級,總爬升噸位約15500噸,最大提升高度113米,是目前世界上技術難度和規(guī)模最大的升船機,堪稱世界最大“船舶電梯”。船舶“坐”這個“電梯”通過三峽大壩,全程只需約40分鐘至1小時。三峽升船機的建成和投入使用,為船只過壩提供了快速通道。
武船集團在中船重工集團公司的統(tǒng)一領導下,承制、安裝了三峽升船機主體設備承船廂結構和承船廂機械設備。針對三峽升船機制造、安裝的特點和難點,武船將三峽升船機分為了結構制造、機械設備制造、結構安裝、機械設備吊裝、機械設備安裝、系統(tǒng)組裝、單機調試、聯(lián)機調試、實船調試、試通航十個階段。武船對各個階段的關鍵技術進行研究分析,研制了大徑鏜孔一體化加工設備、大型螺桿安裝機,確定了大型箱梁精度控制工藝、船廂結構安裝反變形工藝、船廂驅動系統(tǒng)安裝工藝、安全機構、對接鎖定機構安裝工藝等關鍵技術方案,并完成了多項技術創(chuàng)新成果。
武船從2012年10月開始三峽升船機現(xiàn)場安裝,克服了眾多不利因素影響,順利完成了超大型升船機船廂結構及眾多國內首創(chuàng)的相關機械設備的安裝工作。
200米長同步軸系統(tǒng)實現(xiàn)單人手動轉動
2013年底,武船集團完成了三峽升船機試驗,成功完成了三峽升船機驅動機構同步軸系統(tǒng)的安裝和船廂水漏空工況兩項重大試驗。
據(jù)悉,同步軸系統(tǒng)安裝精度要求非常高,在全長200米的長度范圍內,同軸度需達到1毫米,安裝精度之高為國內罕見。在全體員工的不懈努力下,項目部克服種種困難,攻克多個技術難關,成功完成了同步軸系統(tǒng)的安裝任務,且各項安裝精度指標均達到規(guī)定的技術要求,得到了業(yè)主和專家的一致好評。特別是實現(xiàn)了單人手動將全長200米的同步軸系統(tǒng)自由轉動,四個驅動點同時轉到的奇跡,得到了三峽集團公司的高度評價。
船廂水漏空工況試驗是模擬船廂發(fā)生意外事故時,廂內水漏空,以致比平衡重塊輕8500噸,系統(tǒng)平衡被打破,此時安全機構將自主鎖定船廂,從而保證船廂的安全。此次工況試驗非常危險,船廂受拉達8500噸,對船廂結構和安全機構的整體制造安裝質量要求極高。整個試驗過程安全順利,船廂在安全機構的鎖定下,紋絲不動。試驗的成功充分反映了承船廂結構的裝焊質量及安全機構的安裝質量優(yōu)良,從而為三峽升船機的安全運行提供了有力保障。
2015年12月,武船集團完成了首次實船試驗,為了保證升船機的整體運行效率和穩(wěn)定性,武船組織工程技術人員深入研究其控制原理,對三峽升船機的系統(tǒng)調試進一步優(yōu)化,實現(xiàn)三峽升船機眾多機械設備的控制性動作試驗,制定了一套系統(tǒng)性的調試方案,在調試過程中嚴格控制、逐步推進、精益求精,順利完成了實船試航、試通航等多個節(jié)點。
港珠澳大橋六成工程“武漢造”
長波巨浪中“穿針繡花”
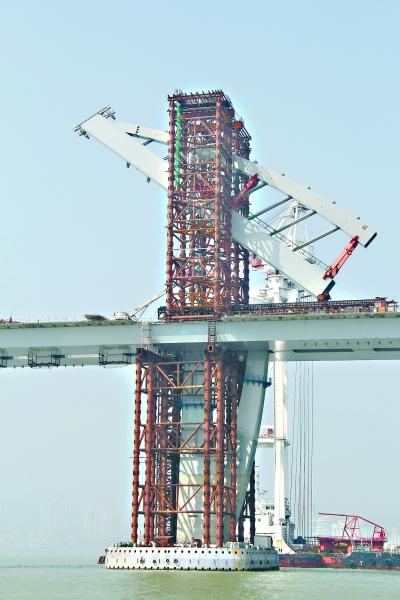
近日,世界最長的跨海大橋——伶仃洋上的港珠澳大橋主體橋梁全線貫通,其設計使用壽命長達120年。在這項超級工程的建設中,武漢近20家企業(yè)參與設計和建設,六成工程“武漢造”。中國頂尖橋隧工程師們在伶仃洋開辟著創(chuàng)新之路,創(chuàng)下了多個世界首次,填補了多項技術空白。日前,長江日報記者走近設計、建設團隊,揭秘不為人知的幕后故事。
“海底山峰”間、澳門機場主航線上作業(yè)
橋梁建設標準高過英美等發(fā)達國家
9月27日,港珠澳大橋主體橋梁貫通當天,中鐵大橋局港珠澳大橋項目經(jīng)理譚國順剛過64歲生日,這也是他在這一項目上度過的第5個生日。他說,自己超齡“服役”,竭盡所能完成了職業(yè)生涯的最后一件作品。這是46年建橋生涯的完美注腳。作為一名中國橋梁建設者,他無比驕傲。
在港珠澳大橋的項目建設中,中鐵大橋局承建了九洲航道橋、非通航孔橋、珠澳口岸人工島連接橋,占海上橋梁段建設的1/3。復雜的海床結構、惡劣的自然環(huán)境、超長的跨海距離每一項,都是巨大挑戰(zhàn)。
伶仃洋是珠江最大的喇叭形河口灣,其下有兩個深海溝。長波涌浪是最大的“攔路虎”。譚國順說,浪涌中,組合梁在吊鉤上來回晃動。一片組合梁重達2000噸,一旦掉下來,橋墩、吊船甚至施工人員都會遭受滅頂之災!“架一片梁所花時間是平時的四五倍?!?/p>
海底,則遍布高強度的孤石,猶如“海底山峰”,打樁成了大難題。
“鉆孔施工中,有3個橋墩都在最后一根樁時遇到孤石,造成鉆頭無法鉆入或孔位傾斜?!敝需F大橋局九洲航道橋工區(qū)副經(jīng)理王義信稱,“800噸的浮吊在風浪大時吊鉤左右擺動可達2米,在這種環(huán)境下作業(yè)就像‘海上繡花’,難度極大。”
26-9號樁長71米,有40米都是孤石,只能用錘頭慢慢砸,花了一個半月才打下去。
如此惡劣的環(huán)境下施工,這座橋梁的建設標準仍是世界最高。譚國順介紹,比如承臺、墩身在工廠里一次性預制,這是世界首次;將幾千噸的大型承臺墩身一起吊裝,埋入海床下,并與樁基精確對接,也是世界首次。
“承臺墩身安裝垂直度偏差要求控制在1/3000之內,而以前的橋梁建設允許1/100;平面偏移要小于1厘米?!弊T國順說,“遠遠高出英美等發(fā)達國家的橋梁標準?!?/p>
此外,大橋局建設的九洲航道橋正處在澳門機場主要航線上,在吊裝重達1168噸的“風帆”造型上塔柱時,不能使用超高的大型吊船吊機。這談何容易?
譚國順說,經(jīng)過技術團隊攻關,發(fā)明了一次性整體“豎轉提升”技術,也是世界首次——將上塔柱整體吊至橋面預先拼裝好的橫移滑道上,利用液壓千斤頂緩慢提升上塔柱,同時沿滑移軌道向前滑移,使其逐步豎轉。
中鐵大橋局二公司工區(qū)總工程師徐瑜回憶,其中一個“風帆”吊裝前,他在現(xiàn)場待了3天3夜,前后沒睡足5個小時。豎轉提升一直從早8時持續(xù)到晚11時。隨著現(xiàn)場指揮一聲“提升到位”,現(xiàn)場一片歡呼,“太激動了!”這一方案的成功實施,填補了國內空白。
500人團隊孤島堅守6年自主
由人體脊椎生發(fā)靈感打破國外技術壟斷
港珠澳大橋島隧工程是世界唯一深埋沉管隧道,也是世界最大沉管隧道,由33節(jié)沉管拼接而成。每節(jié)沉管長180米,重約8萬噸,體量相當于一艘航母。
“如此大規(guī)模的沉管預制,在國內還是第一次,在世界范圍內也沒有多少經(jīng)驗可供借鑒?!敝薪欢骄指壑榘拇髽驆u隧項目總工程師周光強說。
2010年底2011年初,中交二航局項目部踏上珠海外海上的一個荒島——牛頭島,開始沉管預制廠的建設。孤懸大海,沒水沒電,沉管生產(chǎn)所用的各種設備和鋼材、河沙、石料、水泥、添加劑等原材料都靠船從陸上運來。
“我們是摸著石頭過河?!敝芄鈴娬f,為掌握世界最大沉管隧道的預制生產(chǎn)技術,他們曾到荷蘭、日本等公司考察,但對方只提供技術咨詢,核心技術保密?!爱敃r團隊上下眾志成城——一定要自主研發(fā),為中國未來海上超級橋隧工程奠定技術基礎?!?/p>
沉管的混凝土好比人體的脂肪肉身,鋼筋好比骨架。由于鋼筋籠總體硬度偏軟,在沉管足尺模型試驗段鋼筋籠頂推試驗時,變形非常大,穩(wěn)定性差,直接影響安裝精度和預制質量。
一時間,技術團隊犯了難。某天,周光強長期伏案研究后感到后背不適,他下意識地用手扶住了腰,突然靈光乍現(xiàn):人類因為有了脊椎,柔軟的身體才能站得直、坐得穩(wěn),何不在鋼筋籠中加一道“脊椎”?由此,鋼筋籠“勁性骨架”應運而生。新增勁性骨架后,鋼筋籠整體硬度提升,頂推過程中可確保無位移變形。
2012年8月,周光強帶領他的團隊實現(xiàn)了國內海底沉管預制零的突破。最終,整個鋼筋骨架用量相當于一座埃菲爾鐵塔。
中鐵大橋院承擔了島隧工程的施工監(jiān)理。該院港珠澳大橋島隧工程總監(jiān)辦副總監(jiān)蔣偉平說,這33個堪比航空母艦的沉管,要在變幻的洋流里對接,誤差不能超過4厘米,“就如同在大風里穿針”。
從踏上孤島,到今年9月完成16節(jié)管節(jié)預制,管理人員、技術員、一線操作工,500余人在這座島上一待就是近6年,中交二航局承擔了整個海底隧道沉管預制的近半工作量。今年42歲的周光強調侃在島上如同坐牢,這么多年僅回過4次重慶老家。
目前,海底隧道已成功沉放28節(jié)管節(jié),還在繼續(xù)穿越伶仃洋,這艘巨型“航母”的完工指日可待。